Filed under: Small Business, Manufacturing, Entrepreneurs, Sports & Recreation, This Built America

Winter in Hawaii means big wave surf. And on a sunny Tuesday in early December, throngs of fans, tourists and fellow surfers watch as expert watermen charge monster barrel waves, the trademark of the Pipeline break on Oahu's famed North Shore.
It's the first day of trials for the annual Billabong Pipe Masters. Sixteen miles away, inside a small, cramped office, Craig Sugihara, Travis Hashimoto and Glenn Pang huddle around Pang's computer. They are intently watching live coverage of the contest. The guys just have to know how things are going. After all, some of those pro surfers are shredding it on boards the three of them made.
Sugihara started T&C Surf Designs Hawaii 43 years ago in Pearl City, a town in central Oahu located half way between the big town of Honolulu and the country -- which is what the "T" and "C" stand for.
Today, the surfboards are made in the former plantation town of Wahiawa, the gateway to Oahu's North Shore. Hashimoto cuts and Pang shapes polyurethane foam into boards inside the 2,500-square-foot factory tucked at the end of Wahiawa Industrial Complex's row of concrete and cornflower blue sheet metal warehouse buildings. Together they help produce a few thousand surfboards each year for what has become a more than $7 billion global surf industry.
But no matter how big the sport has grown, the Islands are still the soul of surfing.
Surfing's roots stretch back to the ancient Native Hawaiians who rode the waves using wood boards that were often more than 15 feet in length. The sport was especially popular among Hawaii alii (Hawaiian royalty, pronounced ah-lee-ee). In the 20th century, Native Hawaiian Olympic swimmer Duke Kahanamoku popularized the sport through his national and international travels and he is considered the father of modern surfing.
Sugihara, who was born and raised in central Oahu, grew up hearing stories of Duke and watching innovative Waikiki beach boys ride the waves at the surf breaks like the Queen's or Publics. Like many young locals, Sugihara spent countless days after school, and every weekend, riding the swells. Unlike most, he turned his passion for the surf into an international company.
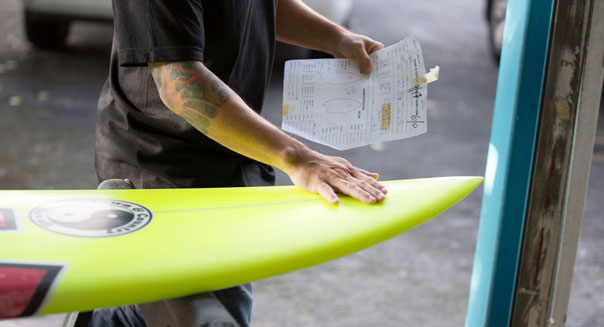
"I've always liked working with my hands," Sugihara says. At the University of Hawaii, he studied industrial arts and planned on becoming a shop teacher. Fate had a different idea.
One day, Sugihara noticed his neighbor's old, yellowing board abandoned in the backyard. "He gave it to me and I stripped the fiberglass off and made a smaller board out of it," he says. At 23, Sugihara crafted his first surfboard.
He was hooked. In between class, Sugihara would head over to Surfboards Makaha in Honolulu and spend hours watching the craftsmen make boards. "I thought maybe if I went there often enough, I'd get a job sweeping the floors, but they never asked me," says the 68-year-old with a soft laugh.
But his determination did pay off with a job at Greg Noll Surfboards, followed by a stint at the now-closed Mystic Surfboards in Waianae on Oahu's west side.
Three years later, Sugihara knew how to cut, shape, laminate -- known in the industry as glassing -- and sand a quality surfboard and he was itching to do it on his own. He had found a location in a shuttered barbershop in Pearl City. He scraped together $2,000 and his father gave him an additional $1,000. In 1971, just four years after refurbishing his neighbor's board, Sugihara founded Town & Country Surf Shop.
That's the greatest joy when someone comes back and tells you your board works really good and you did a great job. It's rewarding.
Making top-notch boards meant long hours for Sugihara in the early days of Town & Country, sometimes all-nighters. For a brief time the shop doubled as his home. "I built a loft above my retail store," he says. "It was a way to have no rent!"
Today, T&C Surf Designs Hawaii has grown into an international company, with seven retail stores, surfboard licensees on both U.S. coasts and company partners in France, South Africa and Australia. Sugihara credits the brand's diversity for the success.
He has branched out from surfboards and sells bodyboards, skateboards, apparel and accessories. Some of its most popular products bear the original logo, the Tao symbol yin and yang. "It means balance," says Sugihara. "In surfing, balance is everything." He says it also represents Oahu's two shores: town, the South Shore and country, the North Shore.
Despite its global success, the Hawaii company still has a small business feel. Sugihara's oldest son Ryan, 36, is the men's buyer and his younger son Gareth, 33, helps part time with sales in the Wahiawa factory. Sugihara's wife Linda formerly ran the apparel division and is now semi-retired. "The boys went to a lot of trade shows growing up and because of our partner in France, my wife got to see the Eiffel Tower," says Sugihara, smiling.
While Sugihara no longer cuts, shapes and glasses the boards, instead overseeing the licensing these days, surfboards remain the heart of the company he started in a modest barbershop. And surfing is still his passion. "I surf with my best friend Allen Wicklund every weekend," he says. "I've been doing that for 40 something years."
Chapter 2: From Blanks to Boards
When Glenn Pang started shaping short surfboards in the mid-1970s, it was a labor intensive and sometimes dangerous profession. "I was doing everything by hand. It was a lot of wear and tear on the body," says the 57-year-old, who grew up on Oahu and lives a few miles from the factory in Wahiawa. After measuring roughly shaped surfboard foam boards, called blanks, Pang used an electric planer to cut the blanks into surfboards and then sand them. "It's this big blade that's spinning," he says, "and pretty heavy, like eight pounds."
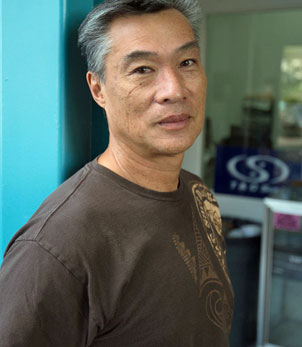
Hashimoto then feeds the blanks into the cutting machine, where it shaves the form down according to the design data. T&C Surf Designs Hawaii uses blanks made in Mexico from the California-based company Arctic Foam.
Hashimoto cuts the blanks into shortboards in 20 minutes. The rest is done by hand; the surfboard making process hasn't changed much since the 1950s because no matter the use of computers, a shaper's hands are still important to finishing a board. Pang deftly smoothes out the thin grooves the machine left behind and finishes the board with sandpaper. Like fresh snow on the ground, fine dust from the foam boards piles at his Croc-strapped feet. Pang wears a mask while working and cleans the boards, and himself, with an air compressor.
Pang can shape about 10 boards each day after honing his craft for the past 40 years. He made his first board at 13. "I watched one of my friend's brothers make a board. I thought, 'that looks fun'," he says. "I was making them in my garage and then started working for Craig in the early '80s. He showed me the ropes." Pang still has the electric blade he once used to cut blanks hanging from one of his workspace's cobalt blue walls, but it's dusty from lack of use.
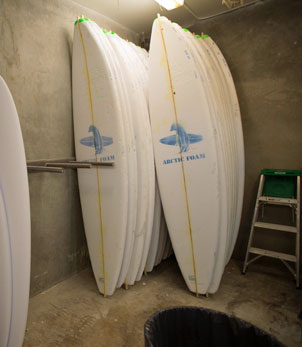
The bright glassing room is lined with sticky, cardboard pieces, as a Monstah glasser delicately wraps a freshly shaped board in fiberglass cloth and applies a thin coat of resin, supplied by Fiberglass Hawaii. The fiberglass gives the board its strength, while maintaining the form. The board then sits to dry on a sawhorse for the next four hours. Next, a crew member from Monstah will seal the lamination during what's called a hotcoat process; it's also when cups for the leash and boxes for the fins are inserted. Lastly, sanders buff off the resin and polish the board, without compromising its strength and integrity. Now it's ready to be sold.
Hashimoto's favorite customers are the beginners. "I like to interact with them and share my knowledge," says Hashimoto, his desk littered with custom orders. "To sell them their first surfboard and they come back and they're super happy about it, it's the best feeling."
But it's the professional surfers who make the most of T&C Surf Designs Hawaii boards. Paddling into intense waves of 10 feet or more, they can break several boards in the process. During the surf season, Pang estimates that surfers competing in the Association of Surfing Professionals circuits cycle through 40 to 50 boards each season. "I think the majority of the good guys get their Hawaii boards from Hawaii shapers," Pang says. "We know the waves." Right now, seven professional surfers ride and represent T&C Surf Designs Hawaii in contests in the Islands.
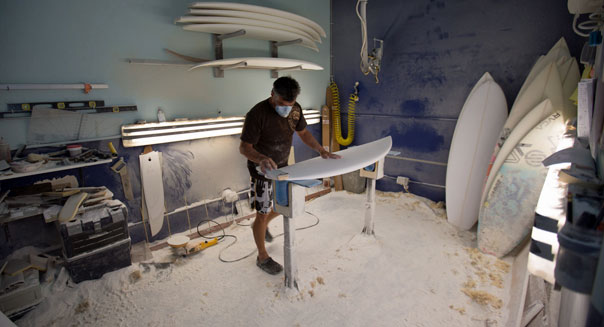
Still he hasn't given up riding waves. He's been a shop team rider ever since he rode for the company's team. And that also means getting out on the water a few times a week with the rest of the factory team at T&C Surf Designs Hawaii. "We get to test out the boards," Hashimoto says. "We have to know what it's about for us to sell it!"
Chapter 3: The Surfer's Stoke
It's not just about the pros for Sugihara. He wanted to give Hawaii's children, or keiki (pronounced kay-key), the opportunity to surf and get their first taste of tournament surfing. So in 1997, he helped start T&C Surf Designs Hawaii Grom Contest (grom is a term for a young surfer).
Sugihara wanted the children to feel the surfer's stoke, he says, and instill a passion for surfing that will last from riding a wave for the first time to a Saturday afternoon session at 68 years old. "When you have parents come up and thank you personally and you see the children have a good time, it's so rewarding," he says. The annual competition is held at Queen's surf break at Kuhio Beach Park in Waikiki and in 2014, approximately 300 groms participated.
Hashimoto was once one of those groms. Born and raised in Ewa Beach on Oahu's West side -- he still lives there and makes the 30-minute commute to the factory -- Hashimoto grew up at the beach. "I bodyboarded, I fished and then when my uncle gave me a surfboard as a kid," he says with a big smile, "I was there everyday."
Hashimoto fondly recalls his experience being recognized as a top keiki surfer with the T&C Surf Designs Hawaii team. "It felt like I made it surfing-wise," he says. He became part of a lifelong community, he says. "Surfing is a big industry and yet we're a small tight knit family; everyone knows each other." As a shop team surfer, Hashimoto has traveled to Japan, Nicaragua, Bali and other exotic surf locales, representing T&C Surf Designs Hawaii. "Town & Country boards are all I know. In the '80s and early '90s it set the trends of what surfboards were all about. Nowadays there's so much competition, but we're still making Hawaii-made surfboards."
Tiffany Hill is a freelance writer based in Honolulu, Hawaii. She has been published in magazines across the state and on the West Coast where she writes about traveling to the Islands, local businesses, education and Native Hawaiian culture and issues. For more, visit www.tiffanyhill.net.
For more Made in the U.S.A. stories, go to This Built America.